Precision Matters: 6 Effective Ways to Limit Human Error in Measurement
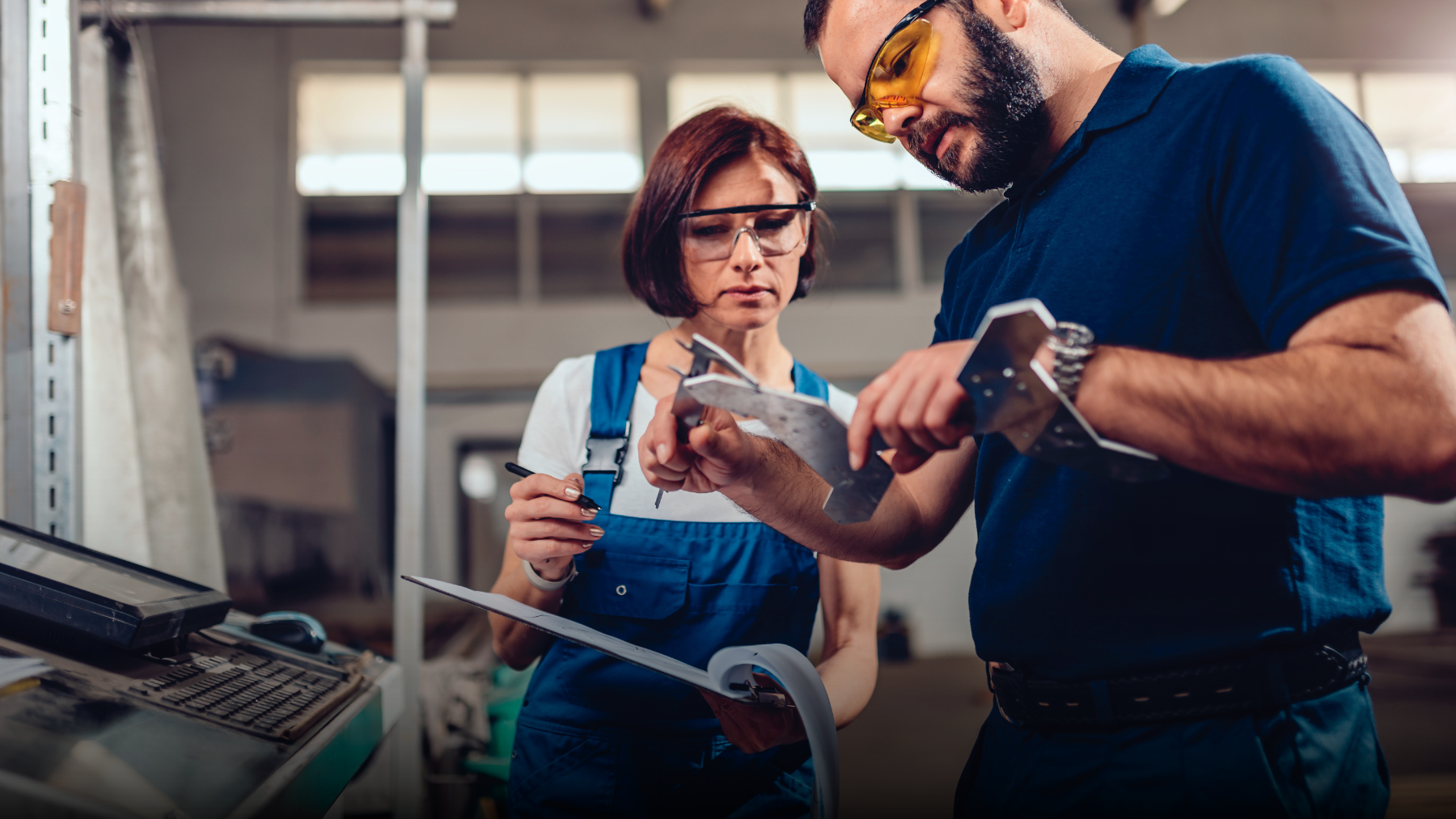
The need for precise measurements is universal, guiding critical decisions and ensuring product quality. But despite our best efforts, human bias influences every measurement. Human error can have far-reaching consequences, ranging from defective products to costly rework and safety hazards. However, if you understand the causes of human error and implement mitigation strategies, you can minimize their impact on measurement accuracy. Here are six strategies to help you limit human error in your measurements.
UNDERSTAND THE CAUSES OF HUMAN ERROR IN MEASUREMENTS
Before diving into prevention strategies, we need to understand the nature of these errors. Potential contributors can include:
- Lack of training: Inadequate training in measurement techniques can lead to errors. Consider an automotive manufacturing plant where workers use precision instruments to measure engine components. Mistakes will likely occur if these workers lack training in measurement tools and techniques.
- Attention to detail: Paying attention to detail is crucial during measurement. Minor oversights or carelessness result in inaccurate findings. Errors may arise from misinterpreting instrument readings, especially when using analog instruments. As an example, parallax errors can occur when the operator’s eye is not in line with the measurement scale, causing an apparent shift in the reading.
- Fatigue and distraction: Fatigue and distractions can interfere with measurement accuracy. Imagine a quality control inspector measuring aircraft part dimensions using a coordinate-measuring machine (CMM)—depending on the criticality of the component, a mistake of just one millimeter could endanger lives. Inspectors who are tired or distracted may miss crucial details, leading to passing non-conforming parts or rejecting a conforming one.
- Personal bias: Avoid personal bias or subjective judgment when taking measurements. Objectivity should always be the goal, following pre-established criteria or standards. Personal biases and expectations can lead to measurement mistakes. For example, if an operator expects a specific result, they may unconsciously skew the measurement process to influence the result.
- Procedural deviations: Neglecting procedures or taking shortcuts can be detrimental. For instance, in a pharmaceutical company, precise measurements of ingredients are vital in drug formulation. Deviating from protocols, even in minor ways, can compromise the composition of medications, potentially affecting patient safety.
SIX EFFECTIVE STRATEGIES TO MINIMIZE HUMAN ERROR
To minimize measurement errors, organizations should implement the following strategies:
1. EXTENSIVE TRAINING PROGRAMS
Establish an extensive training program for technicians who operate measuring equipment. Training ensures all involved clearly understand the principles, techniques, and instruments they use. Theoretical training offers a solid foundation in measurement principles, while hands-on training is crucial in translating theory into practice, enabling them to operate instruments with confidence. Effective training provides the skills required to minimize operator error and is the cornerstone for developing a skilled workforce. Your training program should also consider regular refresher courses to keep your team current on the latest developments in measurement practices.
2. STANDARDIZED OPERATING PROCEDURES
Develop and implement standardized operating procedures for your team. These procedures should define step-by-step instructions for conducting measurements, including instrument calibration, data recording, and quality control checks. Following these standard procedures ensures a consistent approach to measurement. Whether the task is simple or complex, a well-defined process results in fewer mistakes. Accurate measurement lies in the details, and protocol defines those details.
3. ERROR DETECTION AND CORRECTIVE ACTIONS
Incorporate error detection in your measurement process to identify any discrepancies or anomalies. Regular audits, sampling, cross-checks, and validation procedures can catch problems early. These mechanisms not only identify errors but also facilitate corrective action. If errors occur, it is imperative to investigate their root causes to prevent recurrence. When you can pinpoint your measurement issues, you can implement corrective measures and improve your overall process.
4. REDUCE FATIGUE AND DISTRACTIONS
Prioritize measures to reduce fatigue and distractions in the workplace. Encourage your team to take regular breaks and create an environment that fosters your employees’ ability to concentrate. A workplace culture that focuses on employee well-being in these areas will reduce errors caused by distractions, thereby increasing measurement reliability and precision.
5. UTILIZING AUTOMATION AND TECHNOLOGY
Incorporate automation and technology to reduce human error in measurements when practical. Automation eliminates the need for manual entry and calculations, reducing the likelihood of transcription mistakes. Advanced measurement technologies—such as digital sensors or automated systems—improve precision while reducing human involvement. Collaborative technologies make measurements more accurate by removing many sources of human error.
6. CONTINUOUS IMPROVEMENT AND LEARNING
Build a culture of continuous improvement by creating opportunities for employees to give feedback about their experiences. By sharing knowledge and skills among team members, you improve the performance of your entire organization. Host learning sessions, workshops, or conferences often so everyone can learn from one another.
LAST WORDS
Minimizing human error in measurement requires a combination of technology, training, and standards. While it is impossible to eliminate human error, implementing these strategies can significantly reduce their occurrence. In an era where precision is everything, understanding and addressing human influence in measurement accuracy is key to achieving reliable and trustworthy results.
CONTACT US TODAY
At Master Gage & Tool Co, we collaborate with customers to design and implement custom solutions that address their needs. Our wide range of equipment, services, and expertise allow us to improve operations in any industry. As an ISO 17025-certified organization with accredited procedures and experience in custom inspection and customized training, we can provide your employees with the foundation to build your own quality measurement standards.
If you want to learn more about how we can assist you, we invite you to contact us today. Our team is ready to provide you with the information and support you need:
Our Danville Office: (434) 836-4243
Our Greenville Office: (864) 447-5100
Or use our online contact form.